Proteggere le rotelle delle sedie risparmia l’imballaggio
I servoazionamenti Yaskawa garantiscono prestazioni eccezionali
Cercare di risparmiare sugli imballaggi sta diventando una sfida sempre più importante per le aziende, anche quando si tratta di oggetti ingombranti come le sedie da ufficio. Per assicurarsi che queste raggiungano il cliente finale senza aver subito danni, le loro rotelle possono essere protette con cappucci di plastica, eliminando in questo modo la necessità di utilizzare ulteriori cartoni ingombranti. Fondata nel 1879, Gross+Froelich, azienda specializzata nella produzione di ruote a sfera cromate e ruote per mobili, ha deciso di affidarsi totalmente alla moderna tecnologia di automazione per applicare i suoi cappucci protettivi a forma di anello. I servoazionamenti della serie Sigma-7 e un controller della serie SLIO di Yaskawa svolgono un ruolo centrale in questo processo.
Tutto ciò che ha le ruote non deve essere trasportato: questo non significa naturalmente che la tradizionale sedia da ufficio venga spinta fino al cliente, ma le ruote della sedia possono certamente essere utilizzate per trasportarla dal camion al parcheggio e poi fino alla scrivania dell'ufficio. Per garantire che arrivino lì senza graffi, tuttavia, le ruote devono essere protette. Una buona soluzione è rappresentata dai cappucci di plastica che, dopo il trasporto, sono facili da rimuovere e riciclare. Ma come si mettono gli involucri protettivi sulle ruote della sedia?
- Applicazioni
- Picking | Packing
- Assembly
- Client
- Gross+Froelich GmbH & Co. KG
- ARAMIS Maschinenbau GmbH & Co. KG
Fino a 36.000 cappucci al giorno
Ogni ruota montata su una sedia è composta fondamentalmente da due singole ruote, ciascuna delle quali viene dotata di un cappuccio premuto sopra. Questo processo viene eseguito in modo completamente automatico e a notevole velocità. Nella piccola località di Weil der Stadt, in Germania, Gross+Froelich utilizza una macchina prodotta da ARAMIS Maschinenbau GmbH & Co. KG che attualmente opera con tempi di ciclo di 2,4 secondi, dopo la sua riprogettazione con tecnologia servo. A seconda del modello di ruota, vengono applicati alle ruote fino a 36.000 cappucci protettivi a forma di anello – 10.000 in più rispetto alla situazione antecedente la riprogettazione - in modo completamente automatico in 24 ore di funzionamento, e questi vengono successivamente collegati per formare la ruota durante il processo di assemblaggio.
Energia elettrica al posto di quella pneumatica
Sostanzialmente sono bastati solo due interventi per ottenere tempi di ciclo più brevi: la capacità della tavola rotante rotante per i cappucci in plastica è stata aumentata da quattro a otto posizioni. Inoltre, tre degli azionamenti pneumatici installati nella macchina sono stati sostituiti da servoazionamenti elettrici altamente dinamici. Sarebbe stato praticamente impossibile raggiungere le velocità più elevate con azionamenti pneumatici perché lo stress meccanico sarebbe diventato eccessivamente elevato. Inoltre, il livello di consumo di aria compressa è molto inferiore, con un effetto positivo sui costi operativi.
Per quanto riguarda gli azionamenti, Gross+Froelich ha optato per i dispositivi della Sigma-7 di Yaskawa, che già si erano dimostrati validi in molte applicazioni simili e hanno impressionato positivamente il costruttore di macchine ARAMIS. Dopotutto, tra le caratteristiche distintive della serie Sigma-7 spiccano la rapida messa in servizio, l'elevata capacità produttiva e la massima affidabilità operativa. Inoltre, i servomotori AC, estremamente compatti e silenziosi, offrono un'alta risoluzione (con un encoder assoluto a 24 bit integrato) e un'elevata dinamica. Nei servoamplificatori compatti sono anche integrate caratteristiche come la soppressione delle vibrazioni, la soppressione delle frequenze di risonanza della macchina e una funzione tuningless per una semplice messa in servizio.
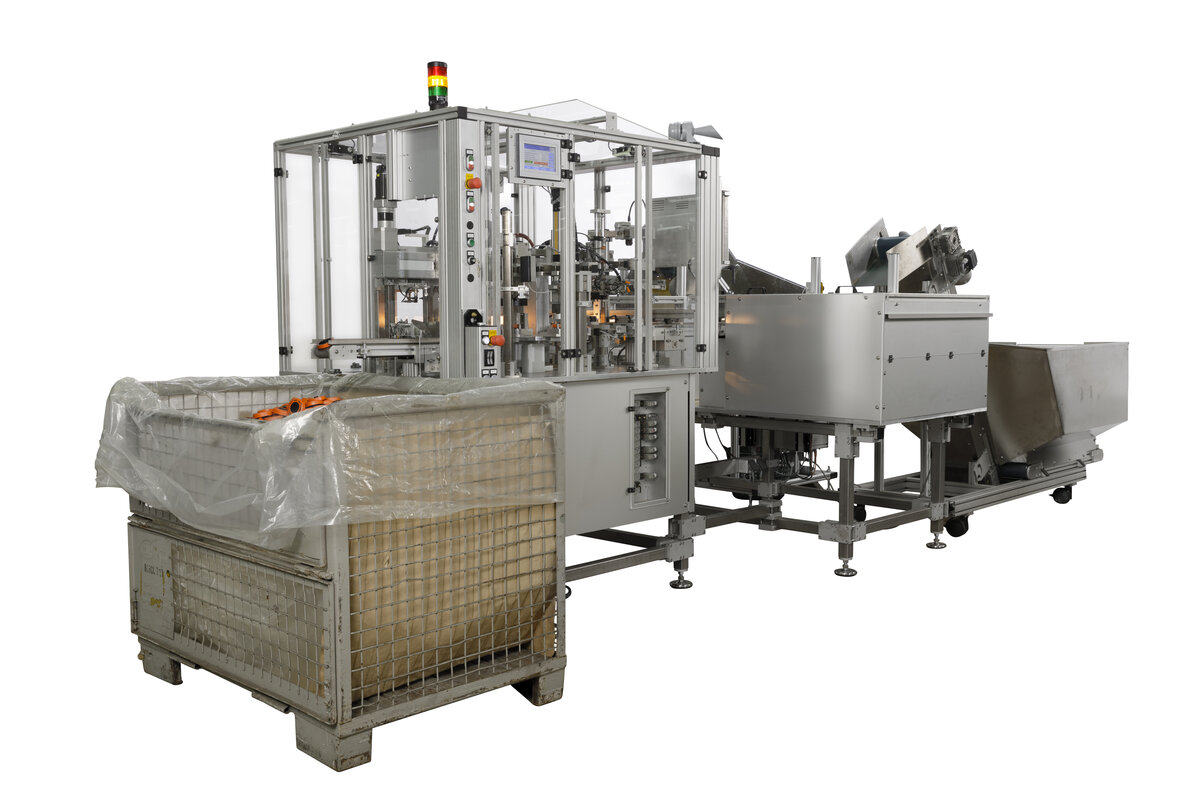
Un totale di tre servoassi da 400 V, ciascuno con 400 W di potenza, sono ora in uso nella macchina e un’unità è responsabile del movimento orizzontale dell'alimentazione. Un'unità lineare pneumatica dotata di pinza trasferisce il cappuccio di plastica dall'unità di separazione all’alloggiamento nella tavola rotante. Un cilindro elettrico azionato da un secondo servoazionamento preme il cappuccio contro il rullo della sedia. Un sensore di forza di compressione rileva il picco di forza quando si innestano e, insieme al sistema di sensori di posizione assoluta sul servomotore, rileva se il processo di pressatura è andato a buon fine. Infine, il terzo servoazionamento controlla il movimento orizzontale necessario a depositare le parti finite sullo scivolo, da cui le ruote, ora protette in maniera adeguata, finiscono in un cassone per essere trasportate ad un’ulteriore postazione di assemblaggio.
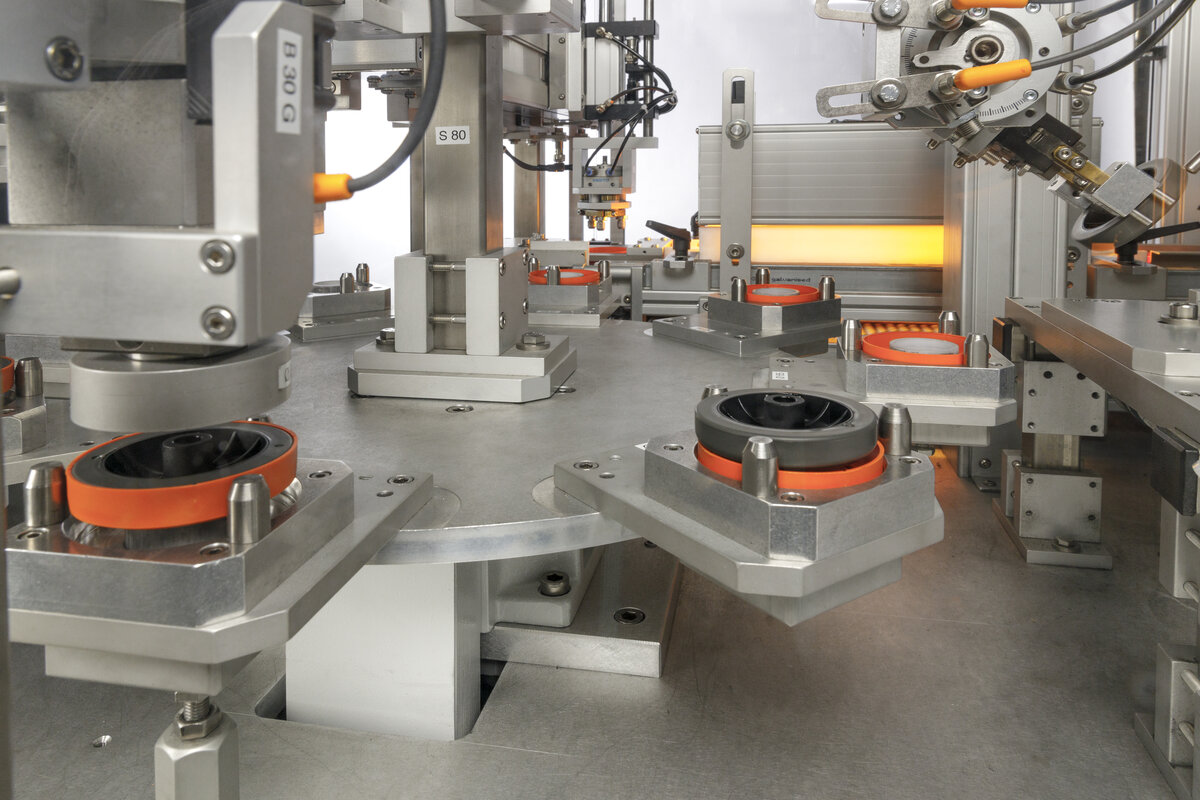
Azionamenti, controller e software da un'unica fonte
Il machine controller della serie SLIO di Yaskawa comunica con i servoassi tramite Profinet e può essere programmato comodamente in Siemens Step7, oltre che adattato efficacemente all'applicazione grazie al suo particolare design modulare. In questo modo, è stato semplice aggiungere e interconnettere i moduli I/O aggiuntivi richiesti; in linea di principio sono possibili anche espansioni successive. Ulteriori vantaggi in termini di velocità sono forniti dal bus backplane del sistema I/O, che funziona a 48 Mbit/s e consente la commutazione con una precisione di temporizzazione di +/-1 μs indipendentemente dal bus di campo. Brevi tempi di ciclo durante l'elaborazione del programma assicurano sequenze rapide mentre l'integrazione nell'applicazione è facilitata anche dall'ampia libreria di sistema dei controller, con un gran numero di funzioni memorizzate che possono essere abilitate secondo necessità. Ciò è particolarmente utile quando si rivedono i progetti originali, soprattutto se si desidera continuare a utilizzare un bus di campo esistente. Profibus è un tipico esempio di tale scenario.
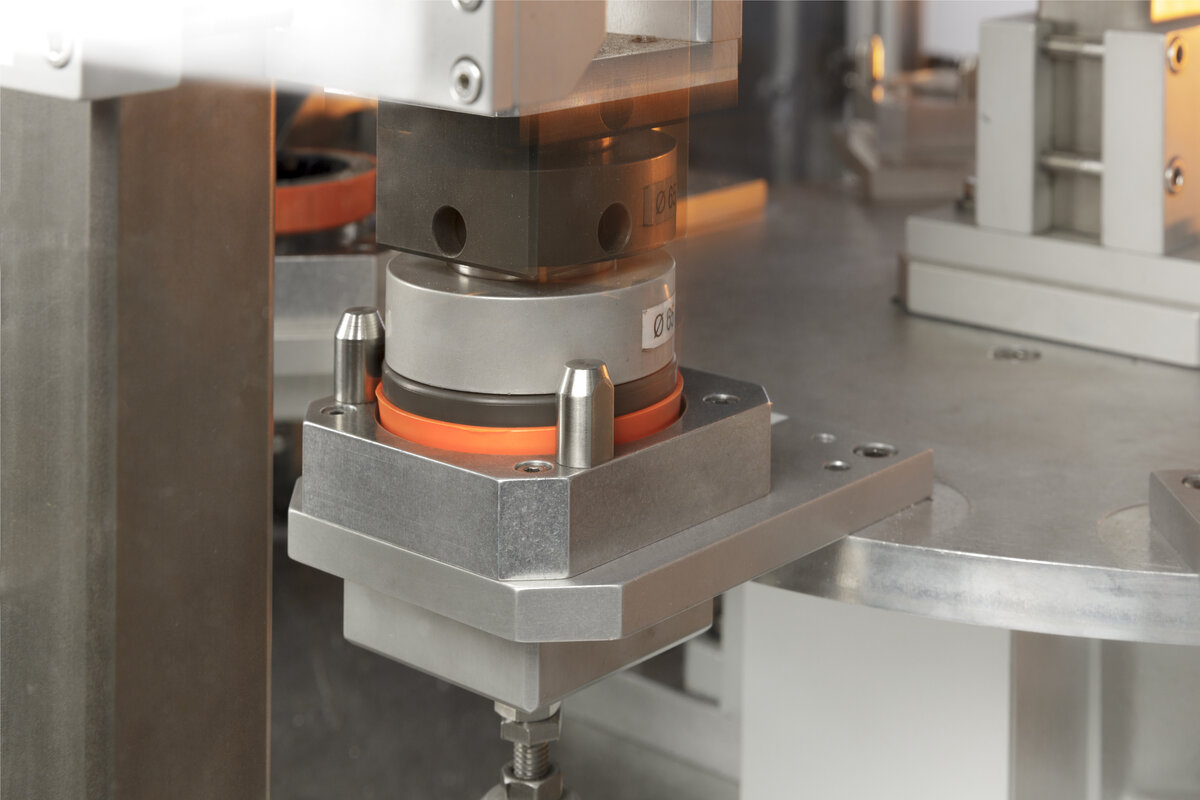
Un altro plus che Gross+Froelich ha riscontrato nella collaborazione con Yaskawa riguarda il prezioso supporto dei tecnici e degli ingegneri dell’azienda, che hanno progettato e seguito passo passo ciascuna fase, in particolare quella di adattamento del software. Ad esempio, hanno contribuito all'integrazione della pneumatica, della visualizzazione e della comunicazione con il sistema di elaborazione delle immagini che Gross+Froelich utilizza per la garanzia della qualità. Il principio di "single source" ha permesso una messa in servizio rapida e semplice in quanto sia l'hardware sia il software sono perfettamente adattati l'uno all'altro e il costruttore della macchina aveva un solo interlocutore. La macchina rimodernata e i componenti installati al suo interno si sono dimostrati validi nell'applicazione pratica, assicurando che innumerevoli ruote per sedie vengano dotate di cappucci protettivi. I servoassi altamente dinamici e il potente controllore compatto stanno dando il loro contributo quotidiano a questo scopo.