Attenzione massima alla salute dei dipendenti
Le misure di ristrutturazione a breve termine nella sede di Unilever a Heilbronn hanno comportato la manutenzione di una grande stazione di pallettizzazione. Invece di personale aggiuntivo, sono stati utilizzati per la prima volta dei cobot - per un periodo di una settimana con un modello di noleggio pratico.
- Industrie
- Packaging
- Consumer goods logistics
- Applicazioni
- Palletizing
- Human-Robot Collaboration
- Client
- Bayer GmbH & Co KG
- Prodotti
- Serie HC
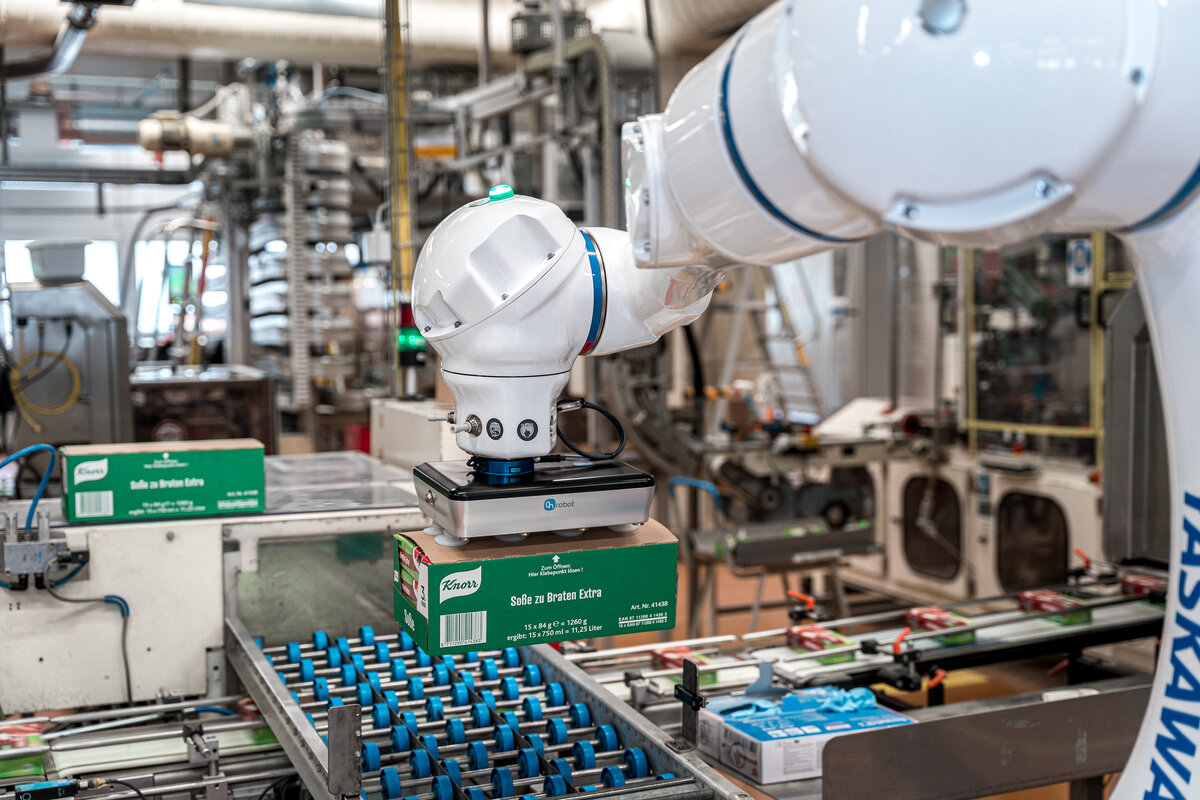
“Per noi la salute dei nostri dipendenti è essenziale, afferma Michael Schenk, responsabile tecnico di Unilever Knorr di Heilbronn, raccontando la scelta aziendale di introdurre dei cobot.
"Di conseguenza risulta per noi fondamentale il tema dell'ergonomia, soprattutto nel settore della pallettizzazione", aggiunge. "Abbiamo visto nei cobot un'opportunità per alleviare efficacemente lo stress dei nostri dipendenti".
L'introduzione di un nuovo telaio ha comportato la chiusura di una delle grandi stazioni di pallettizzazione automatizzata dello stabilimento per una settimana. In passato, in questo caso, si effettuavano anche interventi di manutenzione, ma, ovviamente, i pacchi andavano pallettizzati manualmente, e ciò avveniva facendo affidamento su personale aggiuntivo, finchè Thomas Bittner, specializzato in progetti di automazione presso Unilever, ha deciso di utilizzare per la prima volta i cobot nella primavera del 2023.
"All'epoca ci eravamo già posti la questione se l'uso dei cobot sarebbe stato vantaggioso per noi, anche se avremmo dovuto sostenere delle spese significative", spiega. E aggiunge: “Quando siamo venuti a conoscenza del modello di noleggio di cobot di Bayer abbiamo colto al volo l'occasione ".
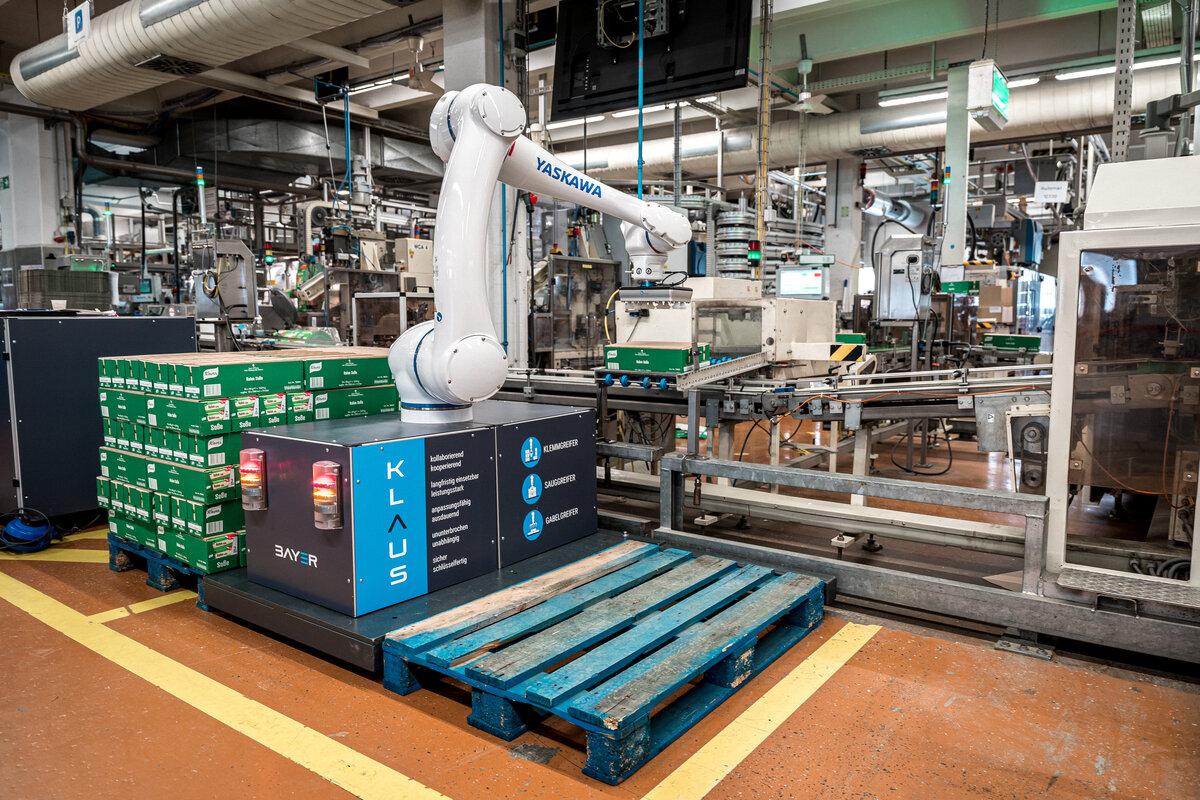
L'ergonomia e la sicurezza operativa sono molto importanti
Nell'area della stazione di pallettizzazione interessata sono presenti macchine riempitrici e cartonatrici. Le confezioni qui prodotte vengono alimentate tramite un nastro trasportatore al sistema di pallettizzazione centrale e poi come pallet finiti al magazzino a scaffalature verticali. Se il processo automatizzato subisce un cambiamento, ad esempio a causa di manutenzione o se viene installata una nuova macchina, alcuni processi devono essere eseguiti manualmente. In questo caso ciò ha significato che su alcune linee i pacchi dovevano essere depositati manualmente: gli addetti preposti prelevano i pacchi a mano, li posizionano sul pallet e un altro addetto li trasporta con un carrello elevatore elettrico fino al sistema di attracco, da dove poi si dirigono al magazzino a scaffalature verticali.
"Per per noi era importante alleggerire lo stress dei nostri dipendenti attraverso l'automazione. E grazie ai cobot ci siamo riusciti".
Per realizzare il progetto, Bittner ha coinvolto gli specialisti dell'automazione della Bayer GmbH & Co KG di Wörnitz in Franconia. Oltre all’offerta attualmente unica di poter noleggiare i cobot per un periodo di tempo limitato, l’esperienza decennale degli ingegneri Bayer nel campo dell’automazione e la vicinanza degli stessi sono stati fattori importanti per prendere una decisione.
"Poiché era la prima volta che utilizzavamo i cobot, che lavorano fianco a fianco con il nostro team e senza barriere di sicurezza, era importante che il fornitore di servizi potesse raggiungerci in brevissimo tempo", afferma Bittner. Oltre all'ergonomia, nello stabilimento Unilever di Heilbronn è anche al tema della sicurezza operativa viene data una straordinaria importanza.
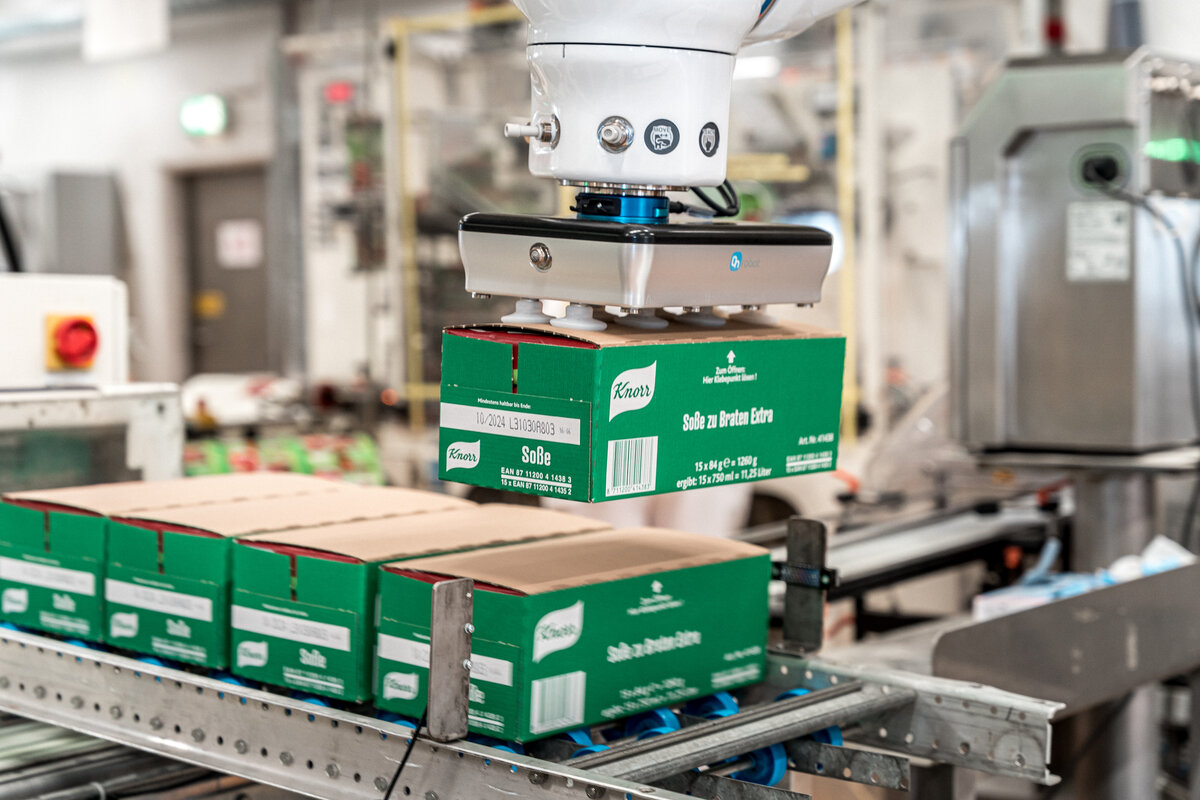
Massima sicurezza grazie all’esperienza
Sin da subito gli ingegneri della Bayer si sono mostrati a disposizione, fornendo persino un’introduzione alla robotica collaborativa spiegando anche i criteri e gli standard di sicurezza in base ai quali vengono utilizzati i cobot. L'attenzione principale è stata rivolta alla linea guida ISO 15066 per i requisiti di sicurezza per i sistemi robotici industriali collaborativi e l'ambiente di lavoro.
Unilever ha deciso di effettuare l'ordine e dopo sole quattro settimane i cobot erano pronti per essere installati. In generale, è la questione della sicurezza uno dei motivi principali per cui molte aziende esitano a utilizzare i cobot. Di fronte alla scarsità di informazioni relative al tema, fornitori esperti come Bayer offrono quindi solitamente una valutazione dei rischi nelle primissime fasi del progetto, sulla base di esempi, se necessario anche nell'ambito di un'ispezione in loco. Inoltre, nei singoli casi nel progetto viene consultato anche un esperto esterno per la sicurezza dei cobot: uno specialista esperto che, come Bayer GmbH, è membro dell'Associazione tedesca di robotica.
Tuttavia, prima della consegna dei cobot, il dipartimento di sicurezza dello stabilimento è stato coinvolto nel progetto e informato in una fase iniziale sul funzionamento dei cobot. Lo stesso vale per la direzione dello stabilimento, del reparto e della produzione, i coordinatori di turno e i dipendenti delle stazioni di pallettizzazione interessate, la maggior parte dei quali ha seguito il progetto con grande interesse e persino entusiasmo. Schenk ha commentato: "Nessuno aveva paura che il cobot potesse portare via posti di lavoro. E non c'è motivo di preoccuparsi perché in realtà il cobot fa solo il lavoro più faticoso e ci sono molti altri compiti da svolgere oltre a depositare i pallet. Alla fine, tutti erano contenti che KLAUS avesse svolto tutto il lavoro pesante così bene".
La positiva valutazione interna del rischio da parte della direzione dello stabilimento e della produzione, nonché la misurazione della forza e un giro di prova prima della messa in funzione dei cobot hanno finalmente eliminato le ultime preoccupazioni che ancora avevano i responsabili della sicurezza e dell'area.
Il Cobot "KLAUS" non necessita di aria compressa
Presso Unilever sono stati installati in totale due cobot Bayer del tipo "KLAUS" (montati su un modello base di Yaskawa), i cui telai sono stati forniti anche a noleggio da Bayer. Gli esclusivi punti di forza del cobot: l'integrazione tubazioni dell'aria che rendono superfua l'aria compressa. In molte altre applicazioni, tuttavia, la situazione è diversa, poiché spesso le confezioni vengono prelevate tramite vuoto con l'ausilio di una ventosa. Nel caso di Unilever, il prelievo dei pacchi è stato tuttavia effettuato elettricamente tramite una pinza robotica di terze parti. La pinza è stata scelta da un esperto ingegnere Bayer in modo tale da non dover utilizzare costosa aria compressa. E poiché si tratta di un prodotto standard, la consegna poteva essere immediata: un altro vantaggio visti i tempi ristretti.
L'installazione è stata effettuata presso quattro stazioni di riempimento e due confezionatrici del sistema di pallettizzazione centrale. Mentre in una stazione venivano assemblati tre pacchi, nell'altra venivano assemblati due pacchi. Normalmente il lavoro viene svolto su tre turni, quindi i cobot hanno preso il posto di sei potenziali dipendenti durante la settimana in cui il pallettizzatore è stato spento.
Sono stati inoltre installati due trasportatori a rulli flessibili da un servizio esterno fornitore, sul quale ciasciun pacco veniva alimentato ai cobot in modo centrato. La centratura gioca un ruolo chiave per quanto riguarda il risparmio di tempo. Se è accurata, il cobot deve solo raccogliere i pacchi e non spostarli avanti e indietro per raggiungerli. È stato risparmiato ancora più tempo facendo lavorare ciascuno dei due cobot su due posizioni pallet. In questo modo, una volta finito un pallet, bastava passare all'altro lato per continuare a lavorare senza interruzioni. Nel frattempo il pallet finito è stato portato via da un dipendente.
Sfida e valutazione del progetto
Prima di mettere in servizio i due cobot, Unilever aveva fornito agli ingegneri Bayer schemi di pallettizzazione, dimensioni del prodotto e informazioni sull’impianto tecnico e i cobot erano già stati programmati in anticipo sulla base di queste informazioni. Una sfida era il tempo ciclo desiderato entro il quale il cobot doveva prelevare i pacchi: un pezzo ogni dieci secondi. Grazie al know-how di programmazione da un lato, ma anche riducendo leggermente la produzione dall'altro, è stato possibile ottenere approssimativamente la frequenza desiderata. Il fatto che la velocità desiderata non potesse essere raggiunta del tutto era dovuto anche al fatto che originariamente era stata prevista una doppia testata, che avrebbe potuto accogliere due pacchi contemporaneamente. Tuttavia, a causa dei tempi ristretti, non è stato possibile attuarlo.
Tuttavia, l’ingegnere di progetto Unilever Thomas Bittner valuta il progetto in modo molto positivo:
"La collaborazione è stata molto buona e Bayer ha risposto in modo estremamente rapido a ogni nostro desiderio. Sappiamo che i tempi per l'intero progetto erano piuttosto ristretti. Insieme a Bayer, tuttavia, abbiamo affrontato questa sfida nel miglior modo possibile. Abbiamo raggiunto ciò che quello che volevamo, ovvero alleviare molte fatiche dei nostri collaboratori". E lo specialista tecnologico di Unilever, Michael Schenk, aggiunge: "Ci siamo resi subito conto, soprattutto durante la messa a punto dei cobot in loco, che i dipendenti Bayer sanno quello che stanno facendo. Hanno molta esperienza e, chiaramente, più esperienza ha qualcuno, tanto più velocemente si riescono a fare le cose”.
Il giorno dell'installazione, gli ingegneri Bayer, gli specialisti di Yaskawa e il produttore di trasportatori a rulli erano sul posto per garantire che i cobot iniziassero bene. I responsabili del progetto presso Unilever hanno sottolineato inoltre che la risposta rapida e la stretta collaborazione tra tutti i soggetti coinvolti sono state estremamente positive. E Bittner aggiunge: "Abbiamo già lavorato con system integrator di diversi fornitori di tecnologie di automazione e devo dire che gli ingegneri Bayer si distinguono chiaramente per la loro velocità, la loro competenza e il loro approccio proattivo."
Conclusione: l'utilizzo dei cobot per la pallettizzazione presso lo stabilimento Unilever di Heilbronn ha avuto un tale successo che l'azienda sta attualmente valutando la possibilità di adottare cobot anche negli altri due stabilimenti che fanno ancora fare a meno della pallettizzazione centrale - e nei quali i pacchi vengono quindi ancora depositati manualmente.
Ma è anche possibile che il modello di noleggio possa essere utilizzato nuovamente anche quando si dovranno eseguire i prossimi lavori di manutenzione. Perché una cosa è chiara, afferma Thomas Bittner: "I cobot hanno permesso di fare anche un grande passo avanti internamente. Perché tutti i manager hanno potuto vedere di persona quanto bene possiamo integrare un cobot nelle nostre operazioni. Ora avere una prospettiva completamente nuova sull'argomento. Questo è qualcosa su cui possiamo basarci. KLAUS ha lasciato un ricordo indelebile."
About Bayer
Bayer GmbH & Co KG è un'azienda con sede a Wörnitz, in Franconia, e opera dal 1999 come partner industriale flessibile nei settori della robotica, dell'ingegneria e del rilevamento 3D con le più moderne apparecchiature di scansione laser. Con circa 50 dipendenti, supporta attivamente aziende di diversi settori nella realizzazione dei loro progetti di automazione. Dalla consulenza e pianificazione all'implementazione e alla messa in servizio finale - e altro ancora. Marchio Bayer: il "sistema di automazione Bayer a 360 gradi". Comprende know-how interconnesso, processi coordinati e tempi di sviluppo brevi.