Afrit introduces more advanced technology into their manufacturing processes
South Africa’s leading trailer and side tipper manufacturer Afrit, has recently introduced the latest equipment and processes available into their manufacturing facility in Rosslyn, north of Pretoria, that will see the company realise substantial efficiency improvements and cost savings in their already technologically advanced capabilities.
In 2019, they began implementing a five-year plan that has a vision to improve its quality and flow within the whole manufacturing environment.
The aforementioned were the main drivers of this investment programme but it was also necessary to add capacity because of the growth that the company was experiencing as well as to drive down production costs while at the same time getting clarity about its manufacturing performance.
It’s one thing introducing and embracing high-end technology but it will have little impact if a company’s production flows and data collection don’t meet the required standards. Afrit is very cognisant of the digital age that we live in and the introduction of Industry 4.0. That becomes irrelevant however if the equipment and processes are not in place to seamlessly integrate with these manufacturing systems.
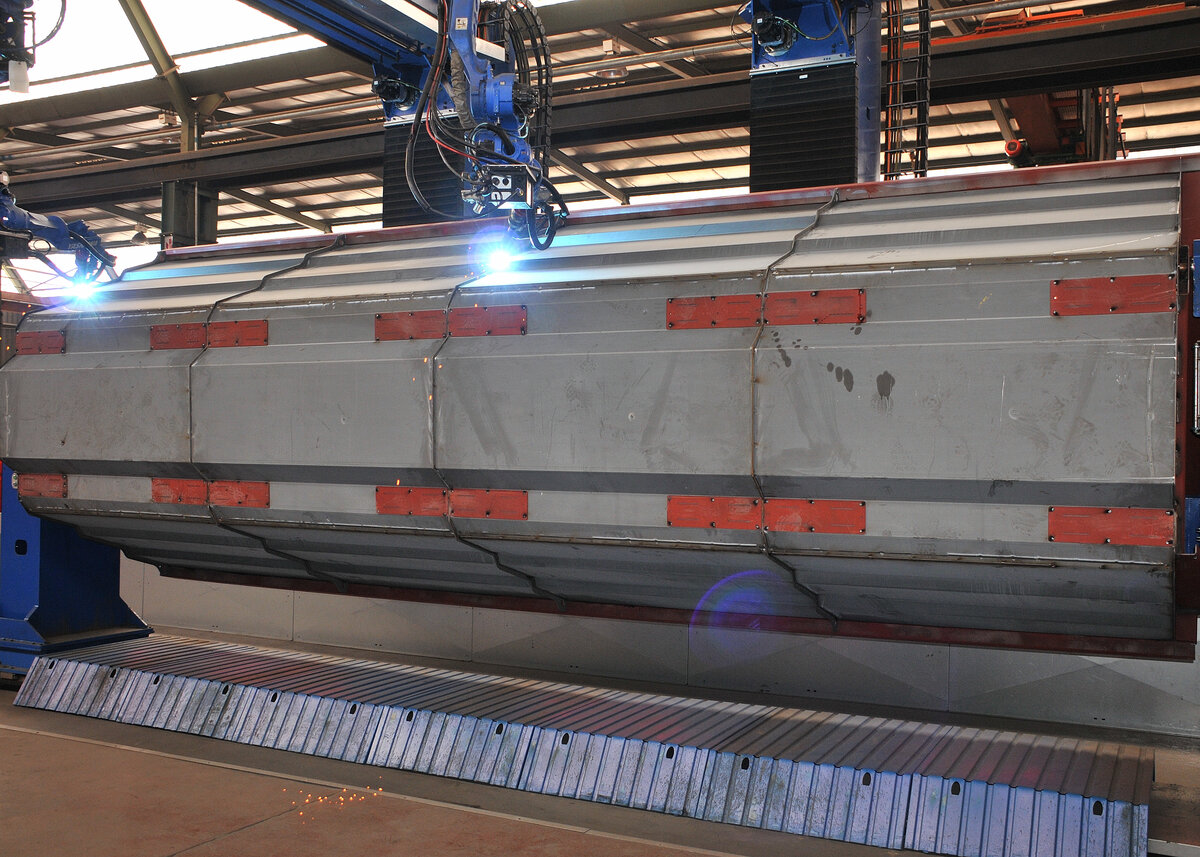
Introduction of a 24-axis Yaskawa MOTOMAN gallow gantry welding system
A great example of this is the introduction of a 24-axis Yaskawa MOTOMAN gallow gantry welding system, a gantry that is designed to provide reliable and accurate welding solutions for the production of very large components such as bins. The two Yaskawa MOTOMAN MA2010 robots have a huge working area. The Z and Y beam travel paths (horizontal and vertical servo axis) are up to 3m and 3.5m, the travel length of the entire system is 24 metres. The support pillars are more than three metres high. We still refer to the system as a gantry even though the robots move along adjustable rails that are secured to the floor. As it is a modular robotic welding system it allows the robots to move along the bins and weld while the two end manipulators will rotate the bins when programmed to do so.”
The two Yaskawa MOTOMAN MA2010 robots have been fitted with cameras so as to monitor and track the seam welding in real time.
Together with the Yaskawa MOTOMAN MA2010 robots, the following equipment was incorporated:
- Delfoi Apexiz offline programming and simulation solution which reduced manual programming man work hours by 80% and programming time by 60%, from two weeks manual to four days offline. Output increased from 8 bins a day to between16 and 20 bins a day. This is real measurement of productivity increases, cost reductions and quality improvements.
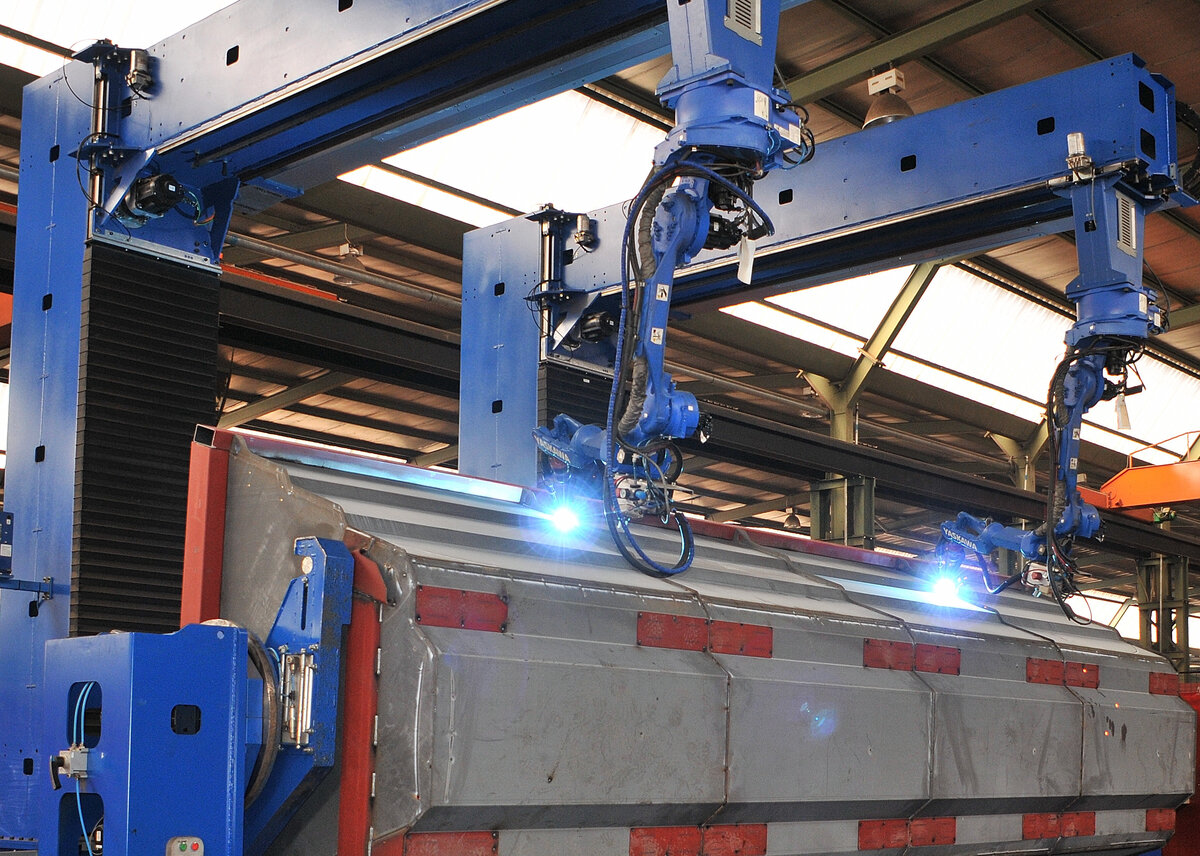
Because the Yaskawa MOTOMAN robotic welding system is modular in design various size bins can be processed for the side tippers.
There are 25 variants of these bins that have to be accommodated and that shows the flexibility of the system.
New factory
Before the other new metal processing equipment were installed, a new 12.500 m² under roof factory had to be constructed to house the new equipment and also to allow the company to move existing equipment into it to optimise the flow of processing material and the resultant processed components. The growth of Afrit has been impressive in recent years and as a result the planning of the manufacturing facilities has been a bit haphazard. During this growth period the company acquired three extra buildings adjacent to the original manufacturing building and together they now comprise about 45.000 m² under roof.
NitraLife nitrogen filtration system
As two lasers are fiber lasers Afrit took the opportunity to pair them with nitrogen-producing generators from NitraLife. The Nitracut nitrogen filtration system filters nitrogen out of compressed air and the high-quality nitrogen gas manufactured provides laser cutting machines with pure laser-cutting-quality nitrogen assist gas.
New BLM LT 8.10 tube fiber laser
An addition to Afrit’s machine pool in the new factory is a BLM LT 8.10 tube fiber laser. This fully automated 3D tube laser cutter is helping to optimise its production processes. For example, the smart software ensures that the machine can be controlled directly from the engineer’s desk so that no more error-sensitive manual operations need to be performed. Fixed predefined control points help achieve an efficient and virtually error-free production process.”
BLM E-Turn 40 all-electric tube bender
Afrit also invested in a BLM E-Turn 40 all-electric tube bender that can bend a variety of tube configurations including round, square, rectangular, flat-sided, oval and elliptical. Tube, with an OD between 6mm and 40 mm, can now be automatically loaded, bent and unloaded.
The accuracy and repeatability of these two machines was an important consideration for the company. However, this has resulted in additional benefits such as reduced setup times, cost reductions per component and enhanced production capabilities in the next step, which is robotic welding of the components processed. The welding jig is now not put under pressure because of the variances in the components that they used to get.
Design
The company now has a different approach to designing its tube components, of which there are 2.293 different variations just of the tube components that they process. They employ 23 engineers in their R&D department are all are trained on PTC’s CREO 3D product design software. They are delighted with the new developments in the processing departments.
Bystronic Xpert 500/5100 press brake
This was the largest press brake that the company has invested in - a Bystronic Xpert 500/5100. The machine has a force of 500 tons, a bending length of 5.100 mm and a throat of 500 mm. It joins the other seven machines in the bending department and they have all been moved and installed in the new building.
Again, this investment was because extra capacity was needed and with the latest technology significant gains can be achieved.
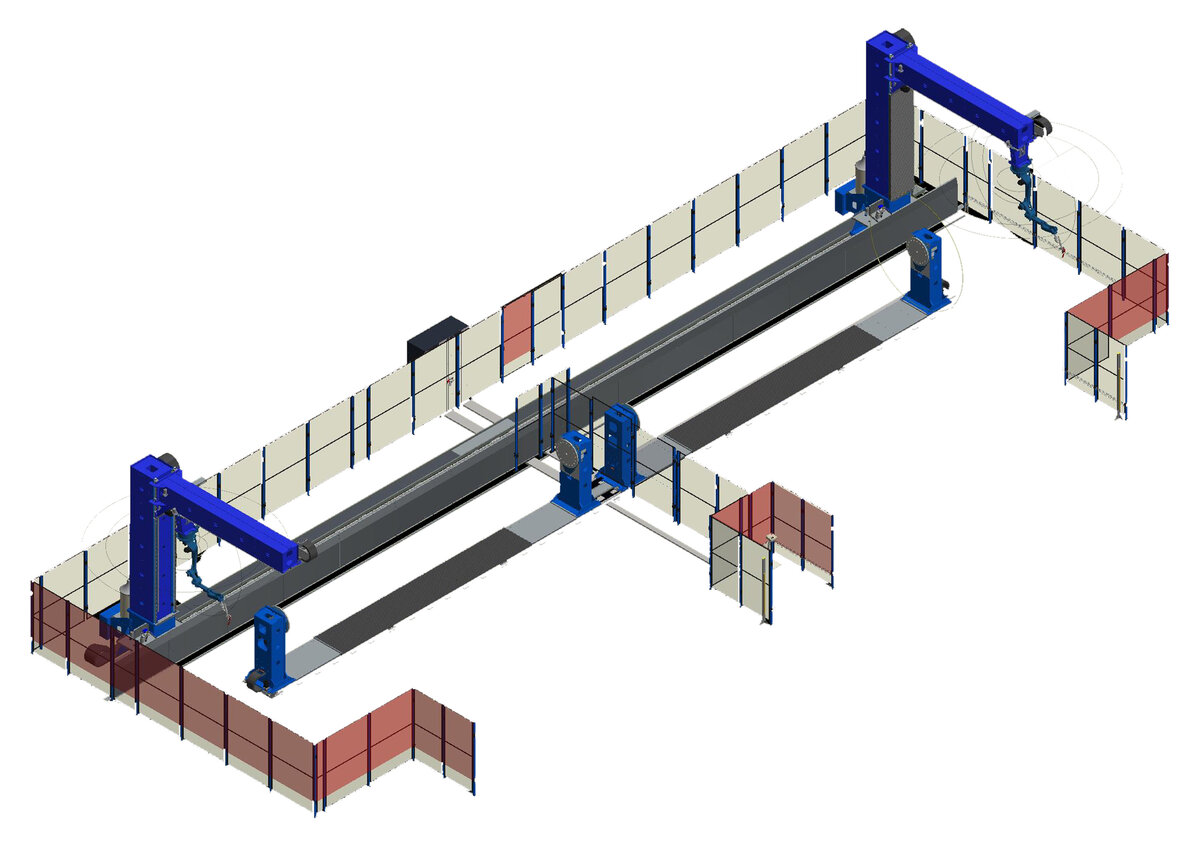
Clarity about Afrit’s manufacturing and process performance
Afrit researched various systems and have now installed a wireless machine monitoring system. Plug-and-play wireless kits were added to existing signal towers to monitor the status and output of machines, equipment and manual workstations. This data is transmitted wirelessly to a receiver connected to an SQL database. The software then compiles the data to produce simple visuals and comprehensive reports at the touch of a button.
This is all done via Wi-Fi and production processes can be monitored and measured in real time and adjustments are made where necessary.
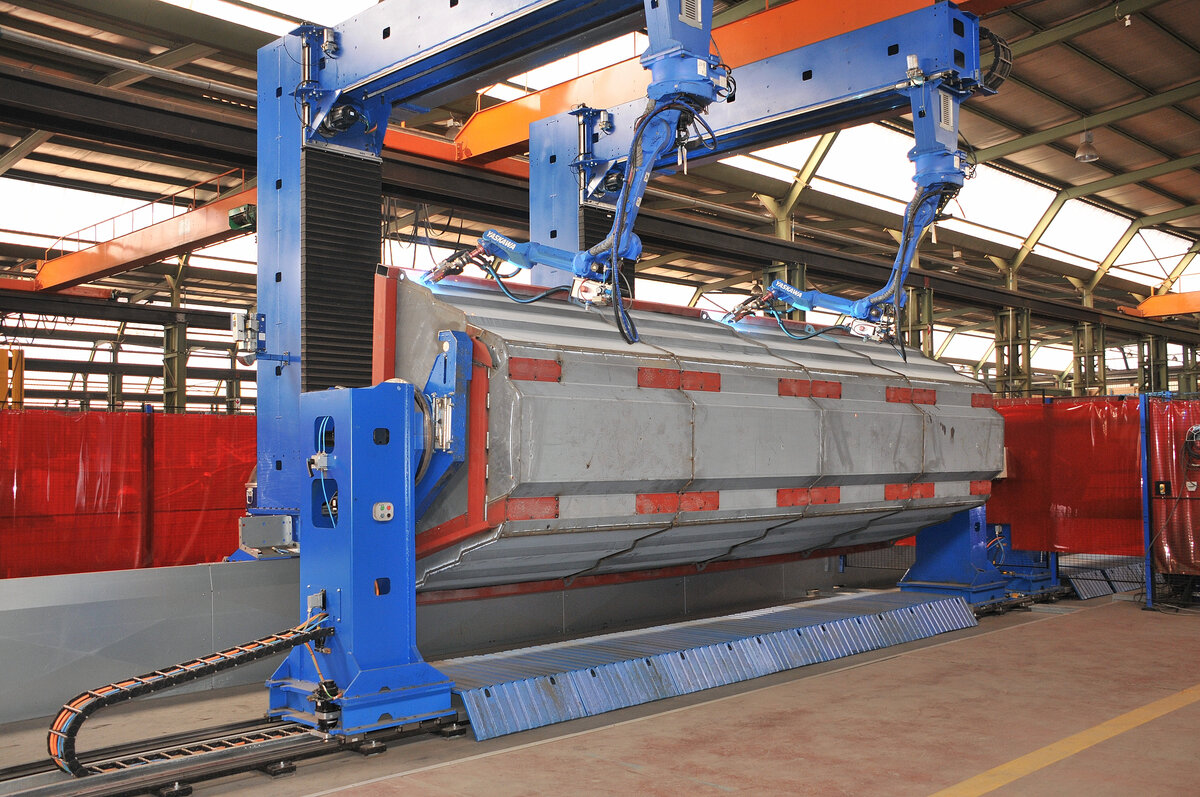
Picture 1
Afrit have introduced a 24-axis Yaskawa MOTOMAN gallow gantry welding system, a gantry that is designed to provide reliable and accurate welding solutions for the production of very large components such as the bins
Picture 2
The two Yaskawa MOTOMAN MA2010 robots have a huge working area. The Z and Y beam travel paths (horizontal and vertical servo axis) are up to 3 m and 3.5 m
Picture 3
The entire Yaskawa MOTOMAN gallow gantry welding system is 24 metres long and the support pillars are more than three metres high
Picture 4
The two Yaskawa MOTOMAN MA2010 robots have been fitted with cameras so as to monitor and track the seam welding in real time. Incorporated into the system is a Delfoi Apexiz offline programming and simulation solution. This software solution, which incorporates sensors and the vision system, transmits the data via Wi-Fi and this then allows the offline programming and simulation to take place remotely
Edited with the permission of https://crawfordpublications.com/metalworking-news/